Scott in PA
Member
Hi All,
I started the restoration of my Fordson Super Major over the weekend. When I started the engine strip down, I noticed a large amount of silicon around the fuel pump. When I removed the fuel pump and silicon, I found a crack on each side of the fuel pump mounting surface. They start at the opening for the pump"s lever and travel out to the edge of the machine surface. After some more examination it appears that at some point in the past, the #4 rod broke and hit the fuel pump area which pushed the block outward and caused the cracks. Neither crack goes all the way through but the block is pushed out about 1/32nd to 1/16th of a inch on the one side.
My question is about how to go about fixing this problem. I have done a fair amount of research on welding cracks in cast iron and have done it in the past with success. Is there a way to "push" the block back into place before I weld the cracks? Or should I just weld the cracks and have the mount machined flat.
Here are
I started the restoration of my Fordson Super Major over the weekend. When I started the engine strip down, I noticed a large amount of silicon around the fuel pump. When I removed the fuel pump and silicon, I found a crack on each side of the fuel pump mounting surface. They start at the opening for the pump"s lever and travel out to the edge of the machine surface. After some more examination it appears that at some point in the past, the #4 rod broke and hit the fuel pump area which pushed the block outward and caused the cracks. Neither crack goes all the way through but the block is pushed out about 1/32nd to 1/16th of a inch on the one side.
My question is about how to go about fixing this problem. I have done a fair amount of research on welding cracks in cast iron and have done it in the past with success. Is there a way to "push" the block back into place before I weld the cracks? Or should I just weld the cracks and have the mount machined flat.
Here are
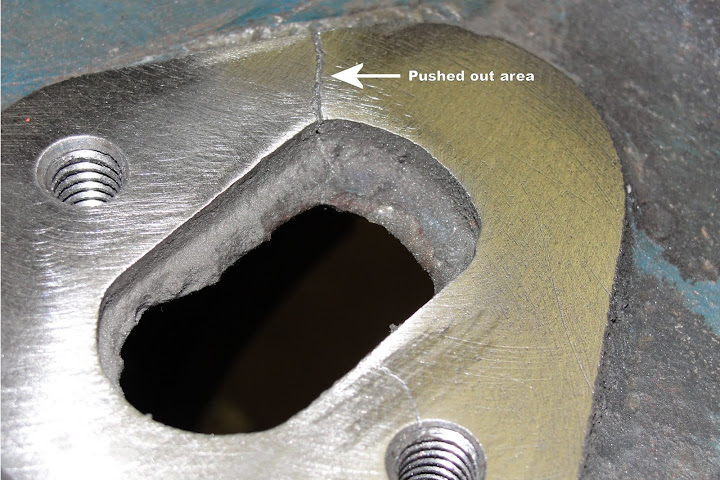
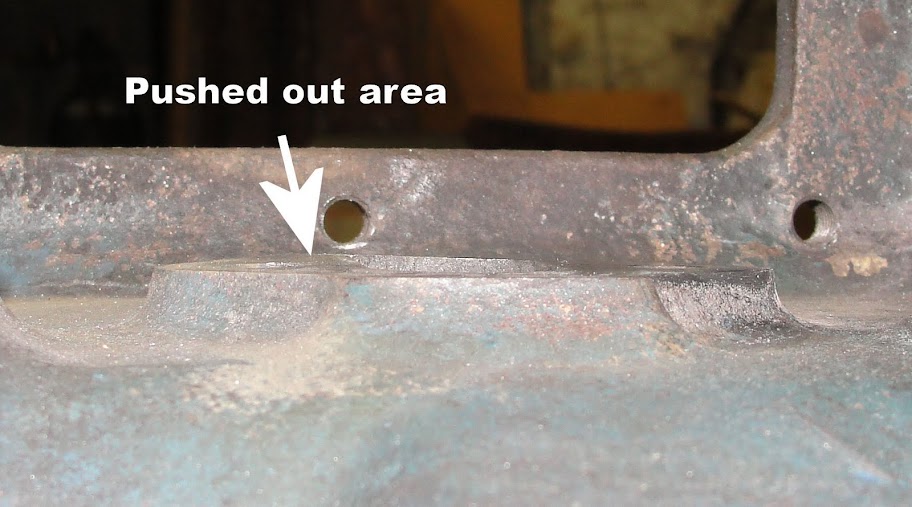