crsutton81
Member
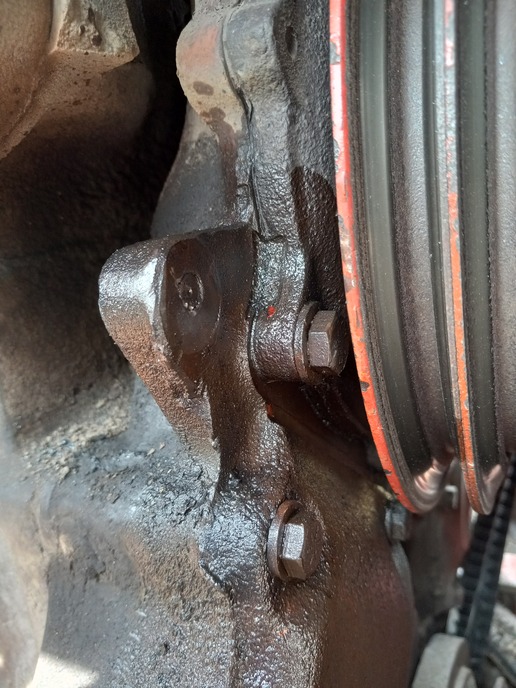
Got a bolt that attaches the top alternator bracket to the tractor that has wrung into. We've tried the trick of welding washers and nuts to the small remaining portion to turn it out with no luck. Also tried taking a drememel tool with a drill bit to drill it out with no luck. There's not enough room to get a regular drill in position. I think the bolt is a grade 8 as everything around it is marked grade 8 also. Any suggestions that doesn't require pulling the radiator and cast iron surrounding to get it out ? I'm afraid there will be more twisted off bolts in the cast iron dealing with it this way.
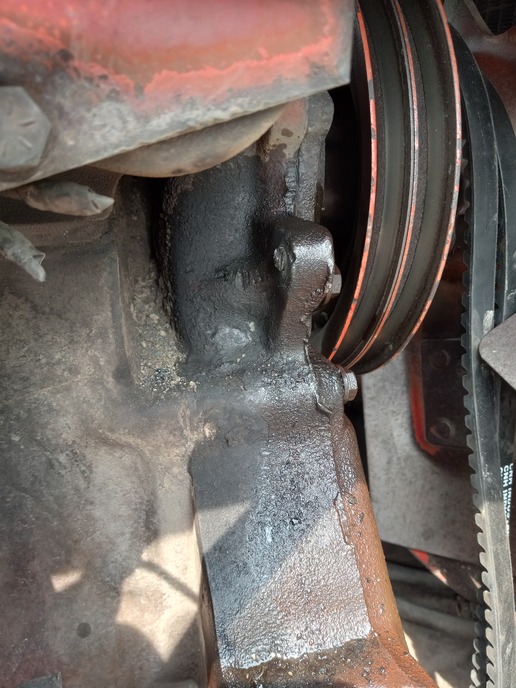