super99
Well-known Member
The blade that I put on my 1850 is sprung. I had to make mounting brackets for it and drill holes to fasten it on. When I pick it up, one side raises a couple of inches before the other side does, it doesn't push level when using it. I need to take one plate off, weld the holes shut, reposition and drill holes again. I have a flat piece of aluminum to lay it on to fill the holes. If I use a stick welder to fill them, will the slag be a problem, or can I just weld until the hole is full and all of the slag will be on top? The holes are 5/8".
When I was working, it was normal to have a hole in the wrong place, so a welder would fill it and grind it smooth and then redrill it, but they used wire welders. I'm wondering if I can do the same with a stick welder or will I have to weld a little , chip it and weld some more??
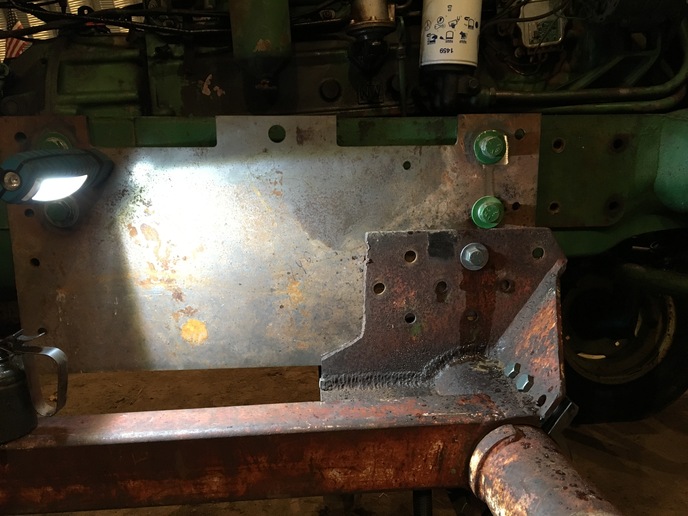
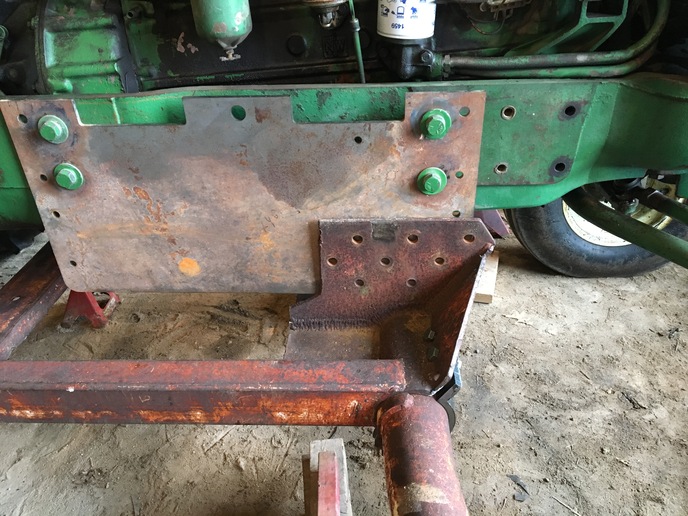
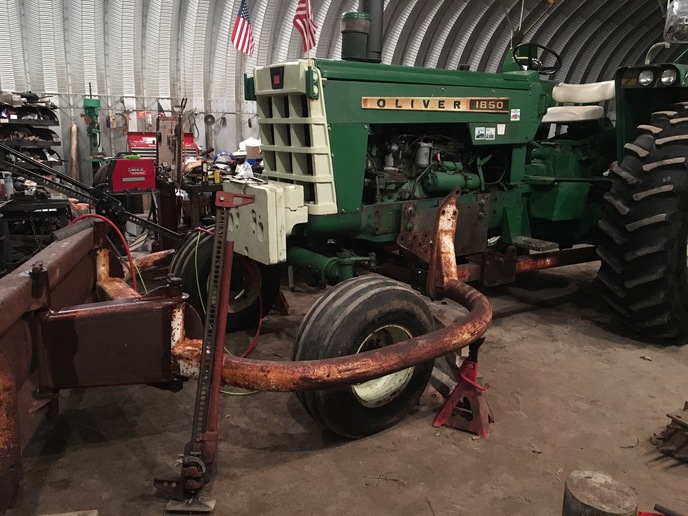
When I was working, it was normal to have a hole in the wrong place, so a welder would fill it and grind it smooth and then redrill it, but they used wire welders. I'm wondering if I can do the same with a stick welder or will I have to weld a little , chip it and weld some more??