super99
Well-known Member
I had to replace the ice door flapper on the refrigerator this morning, so I didn't get back to the blade till after lunch. The homemade brackets that hold the push arms
to the rear axle were too big to use, so I got one side cut down and welded back up and installed this afternoon. Next step is to cut the cross brace off of one side to get the other push bar the same height and then weld it back on and then I can cut the other bracket down and make it fit.
.
Chris
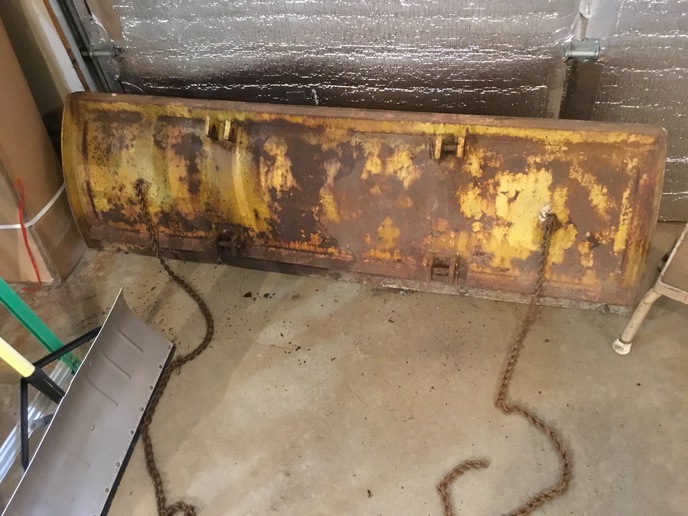
to the rear axle were too big to use, so I got one side cut down and welded back up and installed this afternoon. Next step is to cut the cross brace off of one side to get the other push bar the same height and then weld it back on and then I can cut the other bracket down and make it fit.
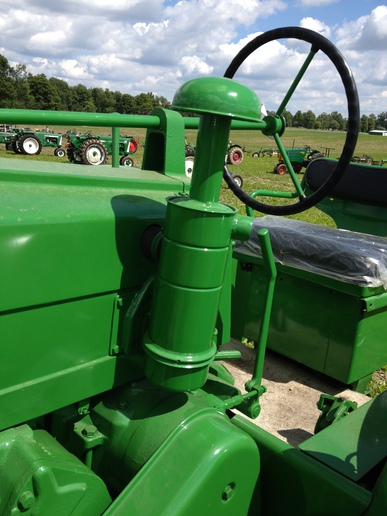
.
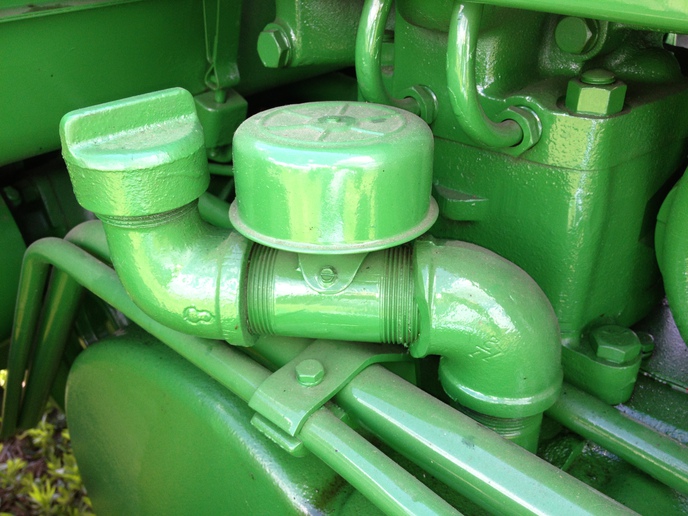
Chris