Brent Zappe
Member
Within this past two years I have moved from a big City area to a small town farming, Ranching and mining area. a place where I always have loved to live in type area. I thought build a work shop on my property would be no problem but threw the years they have changes the rules on what a building has to be. I first thought a metal shop would go but the county says no. soI had to stick to there guide lines in a shop. the first shop was 56 X 32 at the coast of 70.00 a square foot I saw the coast and said sorry can not afford this shop. this next shop plan is 43 X 32 the same price for square foot and so I am going to go with it because I have the money to afford this shop. Like I have said before I am still learning on all this crap on what is okay to build in an area where you live. Strange enough the coast goes by Square footage If I took counters out or walls out it still would not make it any cheaper to build it. The three rooms in the shop are made for equipment like the air compressor, for cleaning engine parts and building engines. Storage on the other stuff needed in the shop like safety stands , floor jacks, Engine cherry picker, and etc. the shop will not house any of my classic cars they have there own garages to go it that is a good thing.
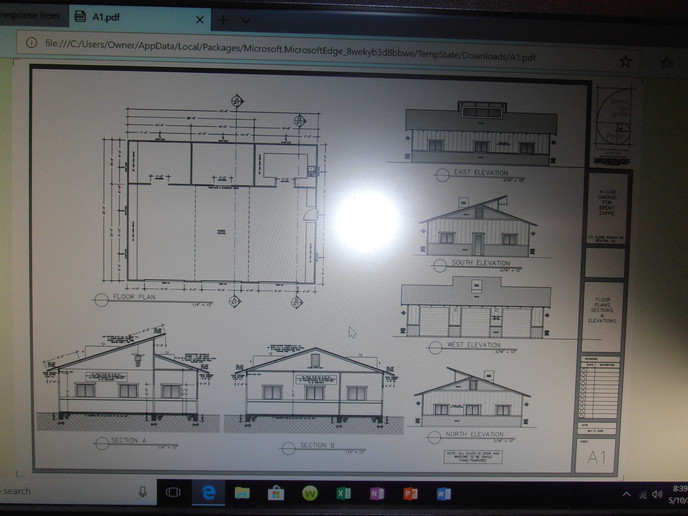