I have needed a way to charge a battery bank at a remote cabin that runs on solar-panels. It is only an issue at times when it has been cloudy for a few days and I have been running a lot of power tools from an inverter.
And yeah, I could use a regular AC input battery charger - but most work poorly hooked to a portable AC generator.
I built a gas-driven battery charger using a new Harbor Freight engine (around 6 max HP) and at first, a 120 amp Delco CS-144. Big mistake. If the battery bank was run down, and I hooked this thing up, the alternator would start charging and the engine would run out of power and quit. Too much alternator, too little engine, and/or not the right pulley ratio for the job.
So, I yanked off the 120 amp alternator and stuck on a 72 mp Delco 12SI I had laying around. Problem is, it already had an aftermarket $10 "self-excite" regulator inside of it to make it a one-wire hookup. I suspected it might be a problem. It was.
Using the voltage-sensing wire can make a big difference in some cases. 10 feet of charge cable leads with #2 copper. I tried charging a solar battery bank with it and got pretty fed up. When charging at high amps - it had 14.2 volts at the alternator output post but only 13.7 volts at the battery bank. The battery bank would never rise above 13.7 volts because the alternator thought it was at 14.2 volts. I finally took the alternator off and stuck in an OEM Delco standard regulator and ran a separate sense wire to the bank with #10 copper. Now it works great and the battery bank comes up over 14 volts. Well great as far as proper charge voltage goes. The engine just barely has enough power to run the alternator at full output. So when I hook it up when the battery bank is run down - it really lug the engine down and near kills it at first. So now I am thinking it needs even a smaller alternator.
The factory built gas-driven DC battery chargers only have 35 amp alternators and maybe now I see why.
I now wish I had one of those little factory built units they used to sell for campers with the lawn mower engines on them.
And yeah, I could use a regular AC input battery charger - but most work poorly hooked to a portable AC generator.
I built a gas-driven battery charger using a new Harbor Freight engine (around 6 max HP) and at first, a 120 amp Delco CS-144. Big mistake. If the battery bank was run down, and I hooked this thing up, the alternator would start charging and the engine would run out of power and quit. Too much alternator, too little engine, and/or not the right pulley ratio for the job.
So, I yanked off the 120 amp alternator and stuck on a 72 mp Delco 12SI I had laying around. Problem is, it already had an aftermarket $10 "self-excite" regulator inside of it to make it a one-wire hookup. I suspected it might be a problem. It was.
Using the voltage-sensing wire can make a big difference in some cases. 10 feet of charge cable leads with #2 copper. I tried charging a solar battery bank with it and got pretty fed up. When charging at high amps - it had 14.2 volts at the alternator output post but only 13.7 volts at the battery bank. The battery bank would never rise above 13.7 volts because the alternator thought it was at 14.2 volts. I finally took the alternator off and stuck in an OEM Delco standard regulator and ran a separate sense wire to the bank with #10 copper. Now it works great and the battery bank comes up over 14 volts. Well great as far as proper charge voltage goes. The engine just barely has enough power to run the alternator at full output. So when I hook it up when the battery bank is run down - it really lug the engine down and near kills it at first. So now I am thinking it needs even a smaller alternator.
The factory built gas-driven DC battery chargers only have 35 amp alternators and maybe now I see why.
I now wish I had one of those little factory built units they used to sell for campers with the lawn mower engines on them.
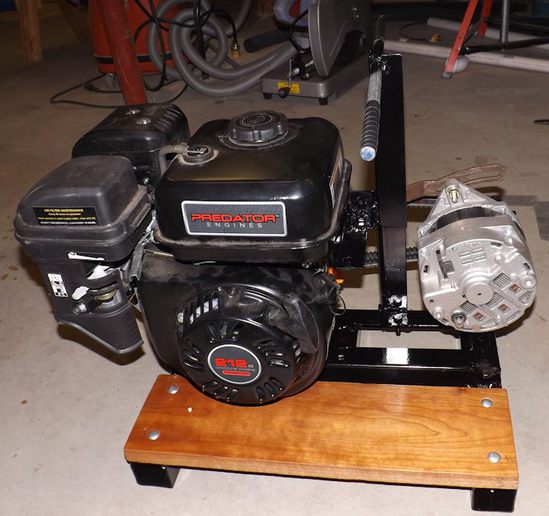
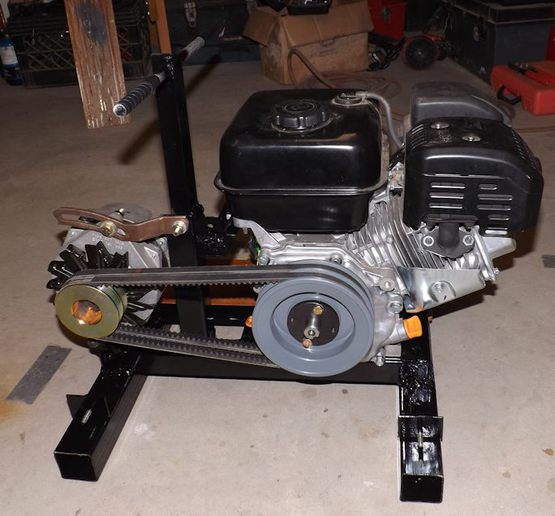
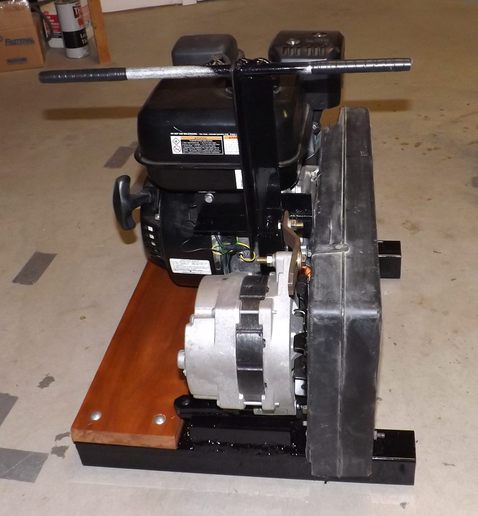
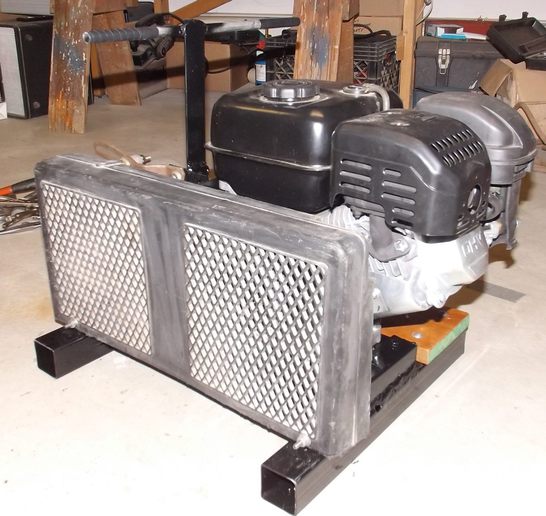
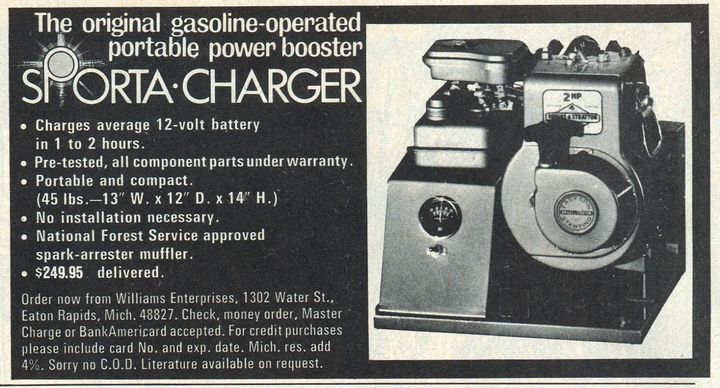
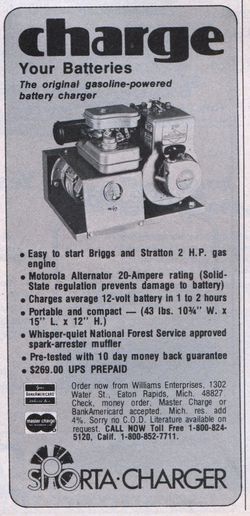