Goose
Well-known Member
Does anyone have any tricks of the trade?
This is the hub on a rear wheel on a D19 Allis. I need to pop it loose to remove the wheel and replace the axle seal. The hub is tapered into the wheel with bolts to draw it tight on the axle. The bolts have been removed. The tire and rim have already been removed for another reason.
Originally, there were special bolts that threaded into the holes to push the tapered hub out of the wheel, but I don't have them, and for all practical purposes there are none around. I'm thinking of maybe cutting three pieces of half inch rod the proper length and screwing 3/4 inch bolts to push against them.
It's entirely possible the hub has not been removed since the tractor left the factory. It's been in our family since 1974, and I don't recall ever having them removed.
Thanks in advance if anyone knows any tricks.
This is the hub on a rear wheel on a D19 Allis. I need to pop it loose to remove the wheel and replace the axle seal. The hub is tapered into the wheel with bolts to draw it tight on the axle. The bolts have been removed. The tire and rim have already been removed for another reason.
Originally, there were special bolts that threaded into the holes to push the tapered hub out of the wheel, but I don't have them, and for all practical purposes there are none around. I'm thinking of maybe cutting three pieces of half inch rod the proper length and screwing 3/4 inch bolts to push against them.
It's entirely possible the hub has not been removed since the tractor left the factory. It's been in our family since 1974, and I don't recall ever having them removed.
Thanks in advance if anyone knows any tricks.
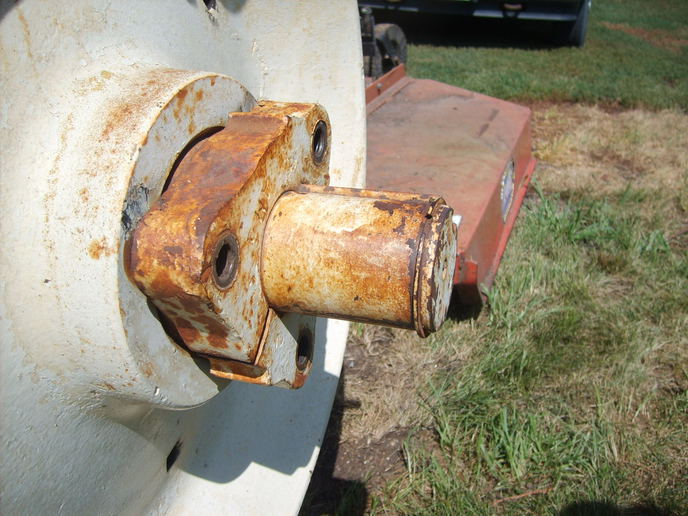