Adrian Billheimer
Well-known Member
Honest opinions please, this piece has been welded by previous owner, it broke beside those welds, I don't think it will hold up for any amount of time if I weld it again.
I was thinking of replacing the piece that goes through the axle tube, but the dimensions don't match any schedule pipe available.
My question is try welding it or find a tractor yard with a good one?
I think having a piece machined would not be cost efective, unless there is something close.
Thanks for any help.
I was thinking of replacing the piece that goes through the axle tube, but the dimensions don't match any schedule pipe available.
My question is try welding it or find a tractor yard with a good one?
I think having a piece machined would not be cost efective, unless there is something close.
Thanks for any help.
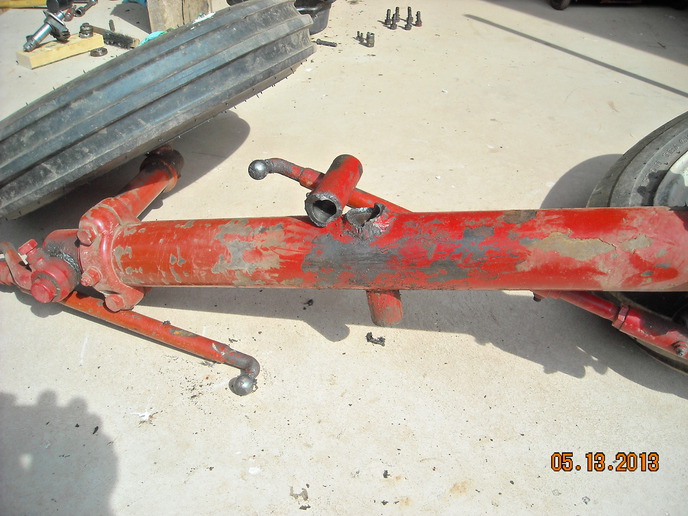