I got 90% of the pieces cut the other day, and clamped together.
actually burned some rods today, and then did a rough fit test to make sure I hadn't screwed up on geometry.
Mind you the welds have not even been chipped or torch marks dressed. wanted to see if she fit up ok, before I did ANY dress work.. wouldn't want to have to torch it apart after dressing it out.. etc..
that said.. it fits good.
added the toplink connection point.
have the rod for the rockshaft ready to cut.
made the links that go from the forward hyd arms to the rockshaft.
have cut out 2 L shaped brackets for the rockshaft, will expirement with various attach points beofre making the holes and welding the plates to the rockshaft.
will have to fabricate some 'clevi' for the lft links ( also rebar ) that go to the 2 salvage 8n lower arms. ( mounted to the lower drawbar bracket.
preliminary measurements and some creative 'eye' work and a lil imagination tells me it 'should' work
we'll see about that wednesday night i guess..
soundguy
actually burned some rods today, and then did a rough fit test to make sure I hadn't screwed up on geometry.
Mind you the welds have not even been chipped or torch marks dressed. wanted to see if she fit up ok, before I did ANY dress work.. wouldn't want to have to torch it apart after dressing it out.. etc..
that said.. it fits good.
added the toplink connection point.
have the rod for the rockshaft ready to cut.
made the links that go from the forward hyd arms to the rockshaft.
have cut out 2 L shaped brackets for the rockshaft, will expirement with various attach points beofre making the holes and welding the plates to the rockshaft.
will have to fabricate some 'clevi' for the lft links ( also rebar ) that go to the 2 salvage 8n lower arms. ( mounted to the lower drawbar bracket.
preliminary measurements and some creative 'eye' work and a lil imagination tells me it 'should' work
we'll see about that wednesday night i guess..
soundguy
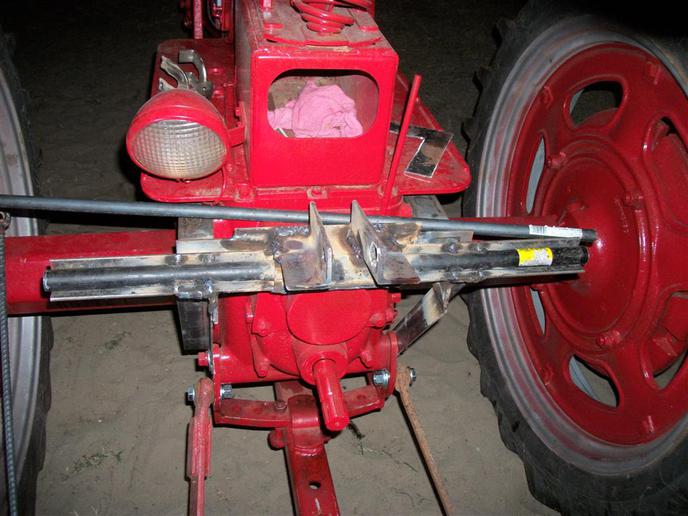
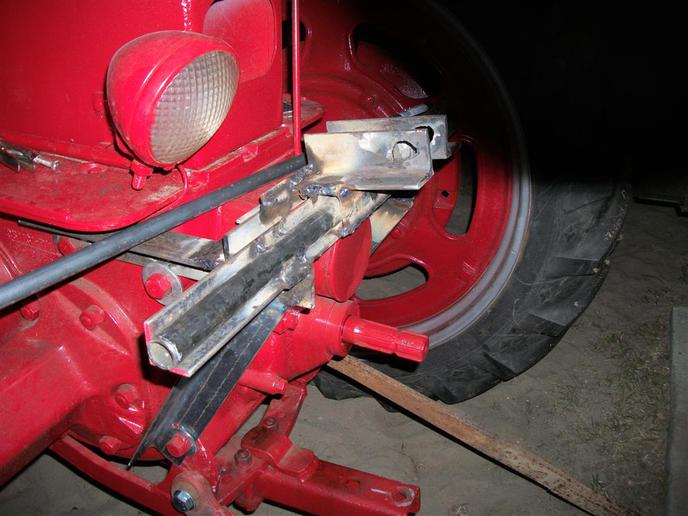
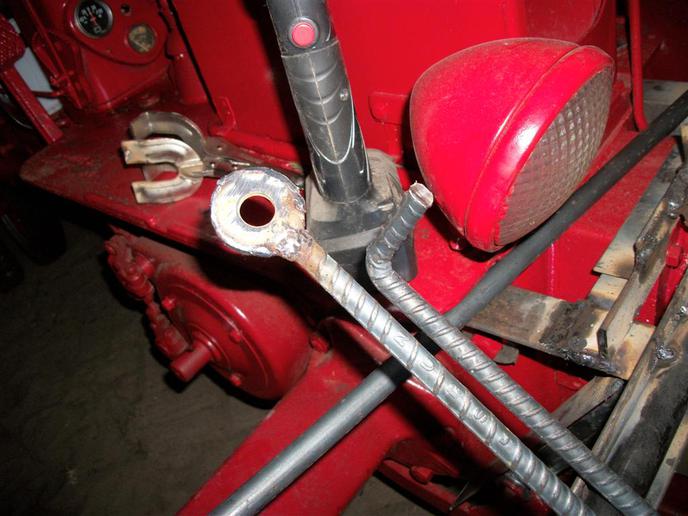
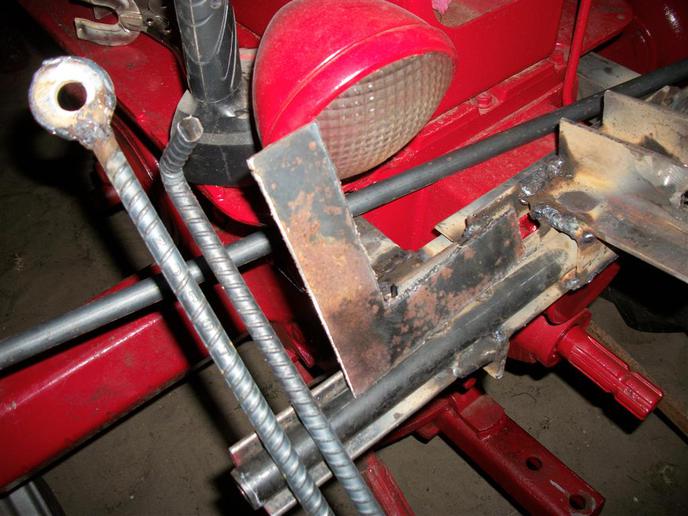
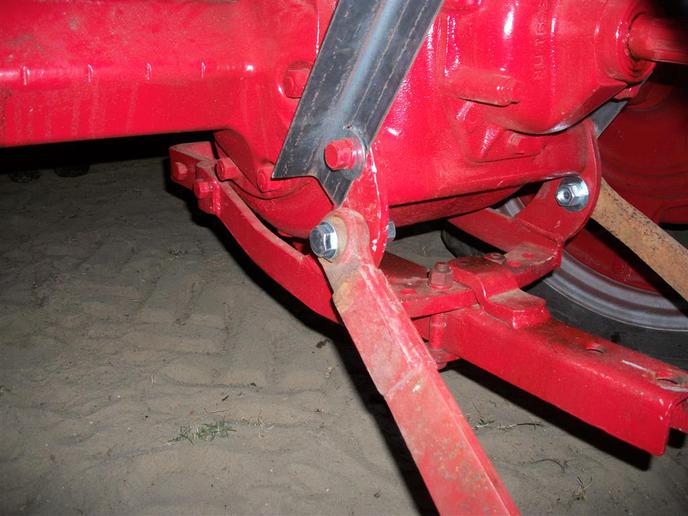