Interesting tractor to work on... got all the way down to the pulley.
still don't see any threads in there
hole is only as deep as the nub on the hand crank. still havn't probed it with a pick to see if it's just packed full of 60 year old crusd that is as hard as cast iron.. etc.
also.. a question on how to adjust that fan belt.. interesting setup on that top hose connection with 3 bolts, and the lil track the fan pulley bolt/sgaft slides in. I didn't take the time to try to disassemble it too much.. just took fan off and the 3 bolts out and se it to the side, see there is a nut in a track on back, thus it cannot turn, and then a nut on the front of that.. it didn't feel like it turned either.. so?? give me some hints on that one.
thanks
soundguy
still don't see any threads in there
also.. a question on how to adjust that fan belt.. interesting setup on that top hose connection with 3 bolts, and the lil track the fan pulley bolt/sgaft slides in. I didn't take the time to try to disassemble it too much.. just took fan off and the 3 bolts out and se it to the side, see there is a nut in a track on back, thus it cannot turn, and then a nut on the front of that.. it didn't feel like it turned either.. so?? give me some hints on that one.
thanks
soundguy
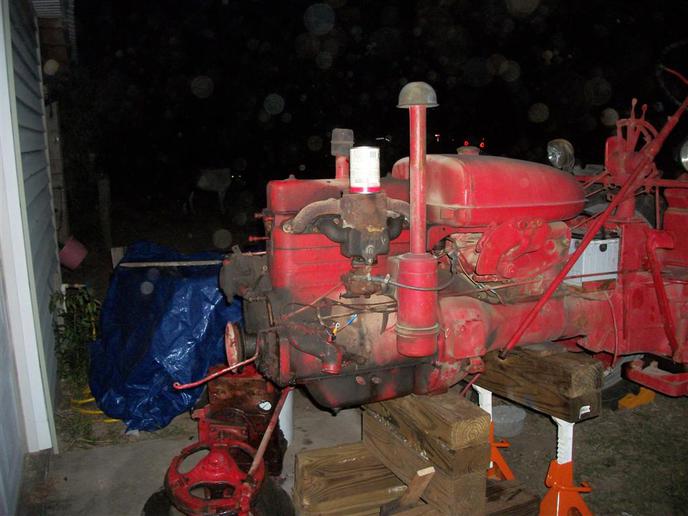
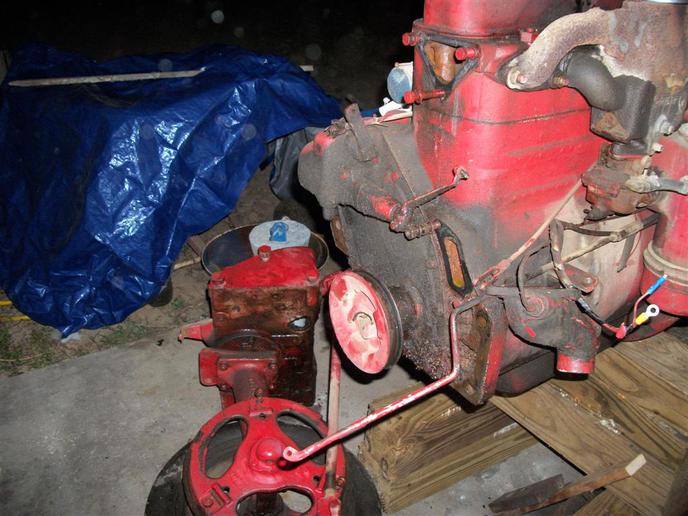