Here are some pictures of the MD as it starts going back together. I know there was some (and always is some) talk about splitting stands. These photos show what I am working with.
It needed a ring gear so it got the clutch split. Then of course there was the "while I am in there" things. The PP was warped so it got a new clutch. The whole thing was COVERED with oil bc of the warped seal retainer. So it got the good seal retainer in place of the old one and a new rear main seal. The pilot bearing was spinning in the flywheel so it got a used flywheel.
I saw today that the top shaft in the trans was possibly leaking so I will change that out. I am also probably going to put the seals in the Lift-All while it is out. I just wish I could make it lift something! Lift-All my...well...you know.
Enjoy!
It needed a ring gear so it got the clutch split. Then of course there was the "while I am in there" things. The PP was warped so it got a new clutch. The whole thing was COVERED with oil bc of the warped seal retainer. So it got the good seal retainer in place of the old one and a new rear main seal. The pilot bearing was spinning in the flywheel so it got a used flywheel.
I saw today that the top shaft in the trans was possibly leaking so I will change that out. I am also probably going to put the seals in the Lift-All while it is out. I just wish I could make it lift something! Lift-All my...well...you know.
Enjoy!
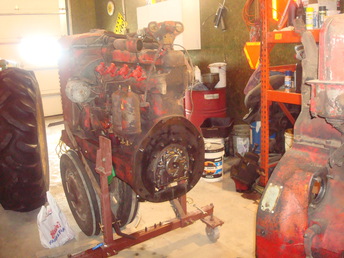
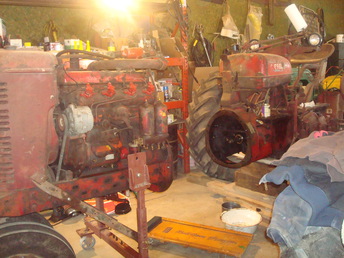